In the business world, especially in the retail industry, an EDI 852 transaction set plays a crucial role in transmitting product activity data between trading partners. In this article, we will explore the details of X12 EDI 852 document, providing you with a comprehensive understanding of its definition, document structure, data elements, and more.
What is EDI 852 Document?
The EDI 852 document, also known as Product Activity Data, is an electronic transaction set used in supply chain management and retail operations for exchanging product-related information between trading partners.
It contains detailed data on the activity of products, such as sales, inventory levels, pricing, and promotions. The EDI 852 document provides valuable insights into product performance and helps in the decision-making process.
Understanding the EDI 852 Document
The EDI 852 document follows the X12 standard format and consists of various segments and data elements that convey specific information. Each segment within the document serves a distinct purpose, such as identifying the product, sales quantities, pricing, and dates.
Typically, retailers provide their suppliers with EDI 852 every week. When automating the EDI 852, the problem is that each retailer may use slightly different formats, data descriptions, and code identifiers.
That is why it is essential to adhere to the EDI 852 specification so that trading partners can ensure uninterrupted data exchange.
What are the Key Components of EDI 852 Document?
The EDI 852 transaction set comprises essential data elements that provide valuable insights into product activity.
The essential components of an EDI 852 document include:
Header: Contains general information about the document, such as sender, receiver, document number, and date.
Line Items: Each line item represents a specific product and includes details like UPC/EAN codes, quantity sold/available, unit prices, dates of sales and promotions, store locations, and much more.
Summary: Provides aggregate information, such as total sales, units shipped, and average prices, at the end of the document.
These elements collectively form a comprehensive dataset that enables accurate analysis and decision-making.
How is an EDI 852 Product Activity Used?
The EDI 852 document serves multiple purposes, including:
Sales Analysis: Retailers can analyze sales patterns by geographical location, identify top-selling products, and measure the effectiveness of promotions.
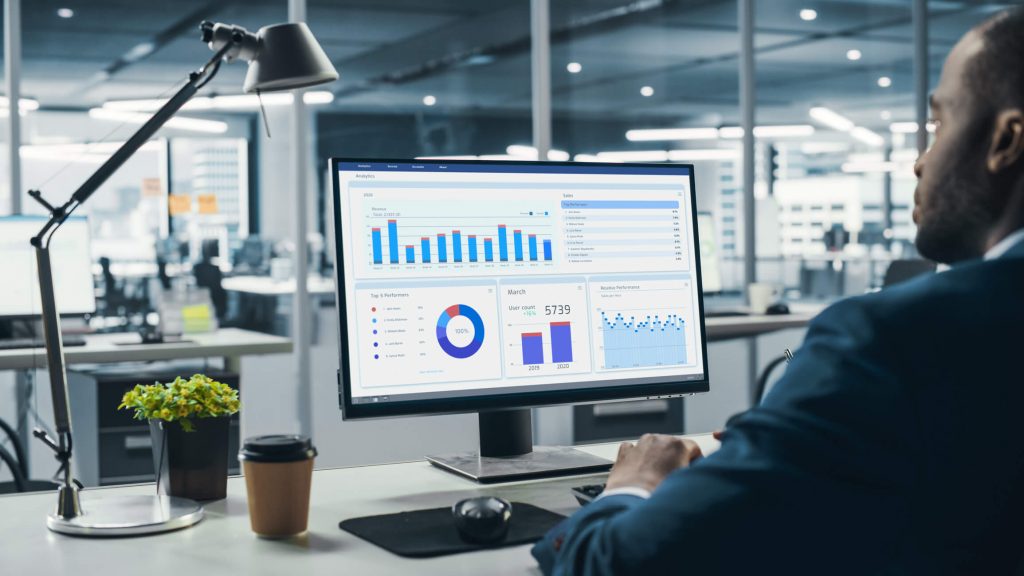
Inventory Management: Suppliers can track product availability, monitor stock levels, and plan replenishments efficiently.
Demand Forecasting: By analyzing historical sales data, businesses can make accurate forecasts and adjust production and inventory strategies accordingly.
Pricing and Promotions: The EDI 852 document helps assess the impact of pricing changes and promotional activities on product performance.
Thus, by leveraging the rich insights derived from EDI 852, organizations can make data-driven decisions and adapt their strategies to achieve business growth.
How is an EDI X12 852 – Product Activity Data Processed?
The EDI X12 852 business flow between trading partners, such as a retailer and a supplier typically follows a standardized process. Here is a general overview of the EDI 852 business flow:
Purchase Order: The retailer generates a purchase order (EDI 850) to communicate their product requirements and submit it to the supplier.
Purchase Order Acknowledgment: The supplier receives the purchase order and responds with an EDI 855 Purchase Order Acknowledgment. This document confirms the receipt and acceptance of the purchase order.
Shipment: When the supplier ships the products, they generate an EDI 856 Advance Ship Notice (ASN) to notify the buyer of the coming shipment. The ASN contains information about the products, packaging, quantities, and carrier details.
Receipt of Goods: The retailer receives the shipment and records the receipt of goods in their internal systems like ERP or CRM.
Invoice Generation: After the retailer receives the shipment and records the receipt of goods, the supplier generates the Invoice (EDI 810) document. The invoice contains the billing details, including itemized charges, payment terms, etc.
Sales and Product Activity: The retailer captures sales and product activity data within their systems. This data includes information such as quantities sold, pricing, promotions, and inventory levels.
EDI 852 Generation: Based on the captured sales and product activity data, the retailer generates the EDI 852 document (Product Activity Data) and sends it to the supplier.
EDI 852 Transmission: Most often, a retailer will transmit an EDI 852 document to a supplier using the services of an EDI provider, such as a fully managed EDI service or an EDI web service.
Supplier Processing: Upon receiving the EDI 852, the supplier verifies, and processes the data. They utilize this information for various purposes, such as sales analysis, inventory management, and demand forecasting.
The retailer and the supplier can integrate the EDI 852 data into their respective internal systems, such as Enterprise Resource Planning (ERP), Customer Relationship Management (CRM), or inventory management systems. This integration ensures seamless data flow, eliminates manual data entry, and enables real-time visibility into product activity.
It’s important to note that the generation of the EDI 852 document typically falls within the retailer’s responsibility. As they capture and analyze the sales and product activity data, they generate the EDI 852 to share that information with the supplier. The supplier then processes this data and utilizes it for their own business purposes.
Which Industries Typically use the EDI 852 Document?
The EDI 852 document is widely utilized in industries such as retail, consumer goods, manufacturing, and distribution. Retailers and suppliers, including e-commerce platforms, department stores, and wholesalers, rely on the EDI 852 to streamline their supply chain processes and optimize inventory management.
What is EDI 852 Message Format and Specification?
The EDI 852 message follows a specific format and specification based on the ANSI X12 standard.
The EDI 852 specification defines the structure, data elements, and guidelines for implementing the document. It outlines the mandatory and optional segments, their formats, and the specific usage requirements. The specification provides a common language for trading partners to exchange product activity data accurately.
The EDI transaction set contains various segments that organize the data into specific categories. Each segment serves a specific purpose and carries relevant data related to product activity.
Here are the key segments typically found in an EDI 852 transaction:
- ST Transaction Set Header
- XQ Reporting Data/Action
- XPO Preassigned Purchase Order Numbers
- N9 Reference Identification
- PER Administrative Communications Contact
- N1 Name
- N2 Additional Name Information
- N3 Address Information
- N4 Geographic Location
- FOB F.O.B. Related Instructions
- TD5 Carrier Details (Routing Sequence/Transit Time)
- DTM Date/Time Reference
- LIN Item Identification
- CTP Pricing Information
- SAC Service, Promotion, Allowance, or Charge Information
- PO4 Item Physical Details
- AMT Monetary Amount
- PAL Pallet Information
- ZA Product Activity Reporting
- QTY Quantity
- CTP Pricing Information
- SDQ Destination Quantity
- G95 Performance Requirements
- CTT Transaction Totals
- SE Transaction Set Trailer
These are some of the common segments found in an EDI 852 transaction set. The specific segments and their usage may vary depending on the implementation and business requirements of the trading partners.
What is the Difference Between EDI 852 and EDI 867?
While both EDI 852 and EDI 867 documents are used for product activity data, they serve different purposes. The EDI 852 focuses on providing detailed information on sales, inventory, and pricing, while the EDI 867 – Product Transfer and Resale Report, is used for transmitting information related to inventory transfers and adjustments between locations or trading partners.
Thus, EDI 867 provides broader visibility into inter-store transfers and resale activities.
By combining the data from both transaction sets, organizations can gain a holistic view of their supply chain, optimize inventory management, and enhance demand planning.
What are the Benefits of EDI 852?
Implementing the EDI 852 document offers several advantages:
Enhanced Data Accuracy. Manual data entry errors are minimized, ensuring reliable and error-free information exchange.
Improved Efficiency. Automation of product-related processes saves time, reduces costs, and enables faster decision-making.
Better Inventory Management. Real-time visibility into product activity helps optimize stock levels, minimize out-of-stock situations, and avoid excess inventory.
Streamlined Collaboration. EDI 852 facilitates seamless communication and collaboration between retailers and suppliers, improving overall supply chain performance.
Thus, implementing EDI 852 streamlines the exchange of product-related information, reduces manual data entry, improves data accuracy, and enhances collaboration between suppliers and retailers.
What Other EDI Transaction Sets Related to EDI 852?
In addition to the EDI 852 transaction set, there are several other EDI documents commonly used in conjunction with or related to EDI 852. Let’s explore some of these transaction sets:
- EDI 846 – Inventory Inquiry/Advice, is used to exchange inventory-related information between trading partners.
- EDI 832 – Price/Sales Catalog, facilitates the exchange of pricing and product catalog information between trading partners.
- EDI 810 – Invoice, is used for transmitting invoice information from suppliers to retailers.
- EDI 850 – Purchase Order, is used to demand of delivery of goods and/or services.
- EDI 855 – Purchase Order Acknowledgment, is used to confirm the receipt and acceptance of purchase orders.
- EDI 867 – Product Transfer and Resale Report.
These are just a few examples of transaction sets related to EDI 852. Depending on specific business requirements and industry practices, there may be other transaction sets that are relevant and commonly used in conjunction with EDI 852 for seamless data interchange and comprehensive supply chain management.
Conclusion: EDI 852 Document for Supply Chain Management
EDI 852 Product Activity Data plays a key role in efficient supply chain management and collaboration between suppliers and retailers. Using EDI 852, organizations can simplify the exchange of product information, improve inventory management, and streamline decision-making. If you have any questions about EDI 852 or EDI in general, please contact our experts for a free consultation.